PRÉSENTATION
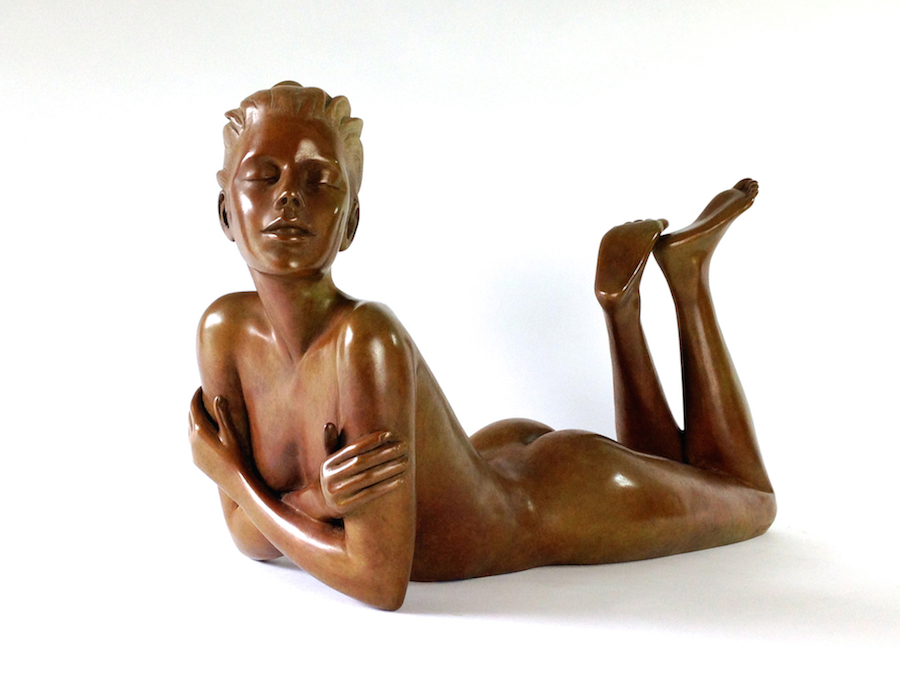
Self-taught sculptor, Alain Choisnet was born in 1962 in Fougères in Brittany.
Very early diversion of objects and sculpture gave an orientation to his creativity.
Having exploited the realistic formalization from various materials, sometimes giving birth to monumental montages whose cohesion of the particles had their weight alone, he now approaches a more expressive figuration.
Bronze, by its warmth and nobility, has become its favorite material to convey a more emotional message.
His artistic approach tends to suggest to the spectator notions inspiring calm and serenity.
Femininity seems to him ideal to communicate these qualities, he wants to offer a soothing vision of the woman with modesty and sensuality.
A sculpture, a story
The bronze sculptures of Alain Choisnet extol the feminine beauty, immortalize a gesture, an emotion, an attitude.
With a natural charm, sometimes youthful, they bathe you in a particular emotion, all in contrast: sensuality, serenity, refinement, poetry.
Each sculpture is a moment of life suspended in time, a story that it seems to want to share with modesty and to continue with the one who contemplates it.
Bronze sculptures
The bronze sculptures presented here received the greatest care during their creation.
When working with clay first, then during the transition to the foundry with its many steps that can immortalize this initial work and sublimate it.
Each sculpture is an original model numbered from 1 to 8, plus 4 artists' proofs (EA I to IV / IV), and a certificate of authenticity accompanies it to its acquisition.
Presented in France, Europe and Asia, Alain Choisnet's bronze sculptures are some of the most beautiful collections of contemporary art.
The sculptor facilitates the acquisition of his works through his online store.
The gallery of the artist in Mougins
Today the artist shares his life between his workshop in Champagne and his gallery in Mougins.
Medalist of the Art-Sciences-Lettres Academy, her collaboration with the prestigious Daum glassworks confirms the quality of her work.
Although represented by galleries in France and Europe, he still favors direct contact during group or personal exhibitions.
By subscribing to his newsletter you will be informed in advance of his next dates and exhibition venues and can discover his latest sculptures.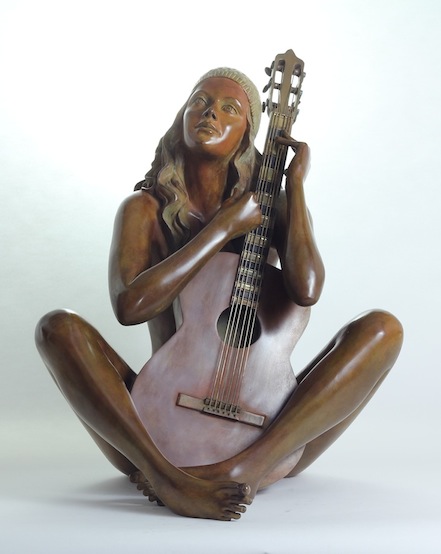
THE METAMORPHOSIS OF A SCULPTURE
Alain Choisnet sculpts his models mainly in clay.
A sculpture may require 100 to 150 hours of work until finished.
Then he entrusts it to an art founder who will turn it into bronze.
Several professions intervene in this realization.
In constant quest for the best quality, he intervenes at different stages of the process in addition to the care provided by the foundry
The technique of casting lost wax bronze
Used for over 5000 years, bronze is an alloy of copper and tin.
Here are the main steps of the so-called "lost wax" technique that allows you to reproduce bronze objects and can vary slightly from one workshop to another. A video illustrates these different phases.
Molding
A first two-part silicone impression is made directly on the clay (sometimes the sculpture is cut and its different parts molded separately).
Plaster is then applied to the silicone to support it so that it does not deform.
The quality of this mold (silicone + plaster) is essential because it will faithfully reproduce all copies of the original model (8 copies + 4 artists' proofs).
The shoe polish
The earth sculpture is then demolded (the clay can be used again to create new models).
The bottom of the mold is carefully waxed with a brush (to avoid air bubbles), then the two parts are assembled.
Liquid wax is poured into the mold so that it lines the walls of the mold, the surplus is evacuated.
This thickness of wax will give the thickness of the future bronze.
At the base of the mold are installed the first supply channels (sticks of wax and resin) which are connected to the wax casting cone (future funnel by which we will sink the bronze).
Then the mold is filled with refractory plaster.
The casting channels and the cone are covered with this plaster.
Retouching
The silicone mold is then opened and the sculpture, which is now waxed with a refractory plaster core, is retouched to rectify the deformations and erase the seal lines of the mold.
Other jets are placed around the sculpture and connected to the channels already in place.
They will allow the molten bronze to propagate in all parts of the second mold in refractory plaster.
A second network is created (the vents), which is not connected to the casting cone, to allow the gases to escape when casting the bronze.
Nails, planted halfway through the sculpture, will hold the core in place inside the mold when the wax has melted.
The hotpot mold
A second mold created around the wax sculpture is called "hotpot mold".
Several layers of refractory plaster are first sprayed to take a very precise impression of the wax.
Then it is coated with the same plaster whose thickness varies according to the size of the sculpture.
steaming
The mold is placed in an oven for 48 hours and the temperature is raised up to 300 ° to evacuate the wax that flows through the different channels (dewaxing).
Then the oven temperature is raised to 600 ° C to bake the hotpot mold and the core, which will have to withstand the casting of molten bronze.
The casting
The refractory mold is buried in a sandbox at the height of the casting cone and then filled with molten bronze at about 1200 ° (depending on the composition of the alloy).
The stall
When the bronze is cooled, the hotpot mold is broken (shake) and the core extracted by fragments from the inside of the sculpture. This mold has only been used once, unlike the first silicone mold which is carefully preserved for subsequent prints.
The channels, now in bronze, are cut and the sculpture cleaned with water jet and sandblasted.
Chasing
There comes the minute step of carving that will correct the imperfections, remove the surplus, plug the holes and resolder between the different parts of the sculptures if necessary, then polish.
The bronze then appears yellow-gold.
The name of the sculptor (if not already registered), the edition number, the stamp of the foundry and the year of creation of the bronze are stamped at the base of the sculpture.
Patina
The bronze containing mainly copper, the humidity of the air will eventually oxidize it, giving it a green color (green of gray) if it is not weathered before its exit of foundry.
The sculpture is therefore hot oxidized using various acids applied with a brush, which will react the bronze giving it different shades depending on the oxidant and the temperature used.
When the desired color is obtained, the oxidation is stopped with a protective coating.
For this we apply a thin layer of wax on the sculpture.
It is finally after being polished and lustrous that the sculpture will reveal all its reliefs,
ready to seduce you!
You can see the works finalized on this site, in the gallery of the artist in Mougins (from May to September) as well as on the art fairs in which he participates.
To know his next exhibition dates, subscribe to his newsletter.
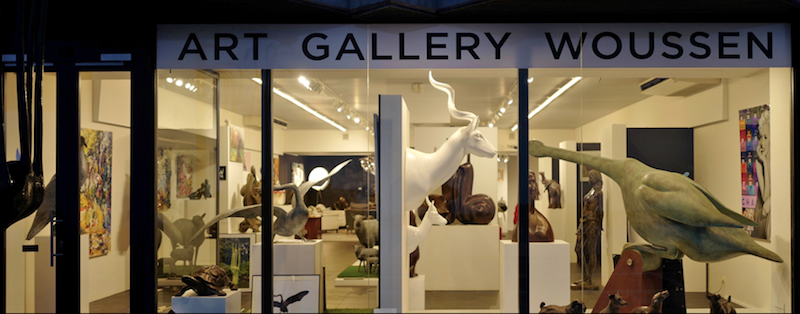
Woussen Art Gallery
Zeedijk 7018300 Knokke
Belgium |